Steam Major Source for heating and electricity generation
The utility of steam is multifold and can be put to use in a variety of industries for multiple purposes. Steam is a secondary source of energy since it is produced from water by combustion of any type of primary source of fuel in a boiler. Steam is produced out of a single process of energy conversion; it is a cheap source of energy.
Following characteristics of steam make it an ideal medium for heat transfer applications:
- Efficient and economical to generate
- Uniform heating - easy to distribute
- Easy to control
- Easily transferred to the process by its own pressure
- Steam plant easy to maintain
- Heat transfer takes place at constant temperature
The applications for steam are heating processes in plants and steam driven turbines in electric power plants, used by the massive petrochemical complexes to the local microbrewery, steam is an integral part of these processes.
Steam is one of the most versatile utility in the industrial energy arena today. In addition to simple heating applications, it can also be deployed in various industrial processes like cleaning, sterilization, drying, concentration, separation and evaporation.
- In culinary applications, it preserves flavours, textures, and retains nutrients. For processing of vegetables and food, steam is used for sterilization and drying under vacuum.
- The use of steam in the industry for the purpose of cleaning does not harm surfaces, motors, bearing seals, sensors and machinery equipment. Hence the requirement of mask off or cover equipment prior to cleaning is not there. There is very less chance of any cross-contamination and thus it helps in faster clean up.
- The freshwater, naturally available from various sources, requires varying degrees of treatment before being fed to the boiler. Treatment of boiler feed water prevents the formation of scales and deposits, removes dissolved gases, protects against corrosion, eliminates water & steam carry-over, optimizes boiler efficiency and minimizes maintenance costs. Improper or nonexistent feed water treatment is the major cause of boiler failure.
- In biotechnology applications, steam is produced in various grades of purity. Steam ranges in purity from boiler grade for routine tasks, to culinary grade “Clean Steam” for food and dairy, and goes up to super pure, pyrogen-free steam for biopharmaceutical and intravenous use.
- In case of “dry saturated steam” there is a definite relationship between temperature and pressure of the steam. This characteristic of steam helps in controlling the processes precisely.
- In the frigid oil & gas fields, steam is used for heat tracing of tanks and pipelines to keep processes moving.
Steam is a safe, flexible, economical, aseptic, and environment-friendly. Steam can be generated through combustion of fossil fuels, biomass or biogas. In the thermal power stations, steam is required to be produced in huge quantity for generation of electricity. The steam has to be produced at very high pressure (>150 kg/cm2) and high temperature (> 5400C), to produce steam in abundance, large volumes of feed water are supplied to the boiler. Although feed water cycle of a thermal power plant is a closed loop process, there is always some loss of water while it moves through the closed cycle. This loss of water has to be made up by addition of treated water into the feed water tank via de-aerator. Feed water contains dissolved oxygen, which can cause corrosion in the boiler tubes. Hence the dissolved oxygen must be removed from the feed water. This process is carried out in the de-aerator with the help of steam. De-oxygenated and heated feed water enters the boiler by means of feed water pump, where it is further treated with chemicals.
Following processes are used for the treatment of water before it is fed into the boiler.
1) Clarification - Raw water with sediments may require a settling tank. Flocculating agents like Alum have to be added to help settling down of colloidal particles and the suspended matter. Clarified water is then drawn off from an outlet near the surface.
Level Indication | Level Switching & Control | Continuous Level Monitoring & Control |
---|---|---|
Tubular Gauges | Float Switches | Capacitance Transmitters |
Float & Board Gauges | Displacer Switches | Hydrostatic Transmitters |
Float & Dial Gauges | Conductivity Switches | Ultrasonic Transmitters |
Float & Tape Gauges | Capacitance Switches | TDR Radar Transmitters |
2) Coarse and Fine Filtration - Suspended solid impurities which have not settled down during clarification are reduced or eliminated by passing make-up water through a filter. If the suspended solids are very fine, a flocculation step may be required.
Continuous Level Monitoring & Control |
---|
Ultrasonic Transmitters |
FMCW Radar Transmitters |
3) Water Softening - Scaling is formed in the boiler tubes and steam related equipment because of minerals deposition which is calcium and magnesium, resulting in costly repairs, increased energy consumption, and plugged equipment. Softening occurs as minerals causing hardness attach to the softening resin and “exchange” for sodium.
Level Indication | Level Switching & Control | Continuous Level Monitoring & Control |
---|---|---|
Tubular Gauges | Float Switches | Capacitance Transmitters |
Magnetic Gauges | Displacer Switches | TDR Radar Transmitters |
4) De-mineralization - De-mineralization is typically an ion exchange process whereby minerals or mineral salts are removed from the water. The process consists of Anion exchanger, Cation exchanger and mixed bed units. The resin-beds in the exchanges have to be re-generated, periodically by passing acid and alkali solutions through the resin-beds.
Level Switching & Control | Continuous Level Monitoring & Control |
---|---|
Float Switches | Float Transmitters |
Displacer Switches | TDR Radar Transmitters |
5) Storage Tank - The treated make-up water is kept in the storage tank, from where it can be fed into the de-aerator and feed tank as per requirement of the make-up water.
Level Indication | Level Switching & Control | Continuous Level Monitoring & Control |
---|---|---|
Tubular Gauges | Float Switches | Ultrasonic Transmitters |
Reflex Gauges | Displacer Switches | TDR Radar Transmitters |
Magnetic Gauges | - | FMCW Radar Transmitters |
C.N Shukla, Training & Development Consultant, Pune Techtrol.
He is an integral part of organization and provides best industrial training building a technically strong team.
For further information on level measurement and control instruments, contact our experts on +91-20-66342900 or mail us at ho@punetechtrol.com
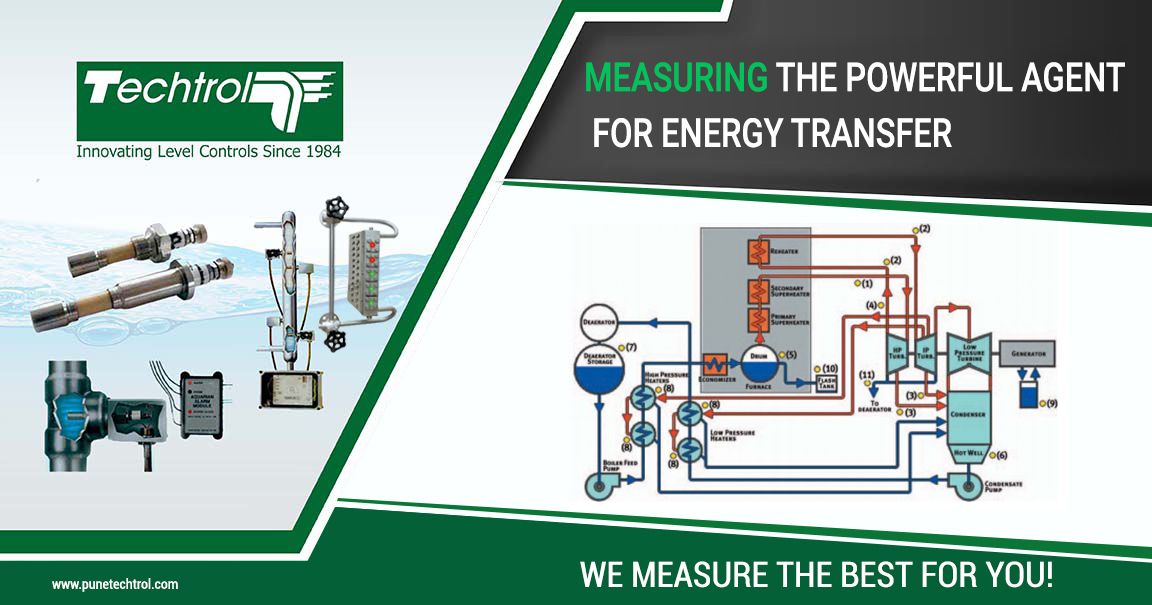